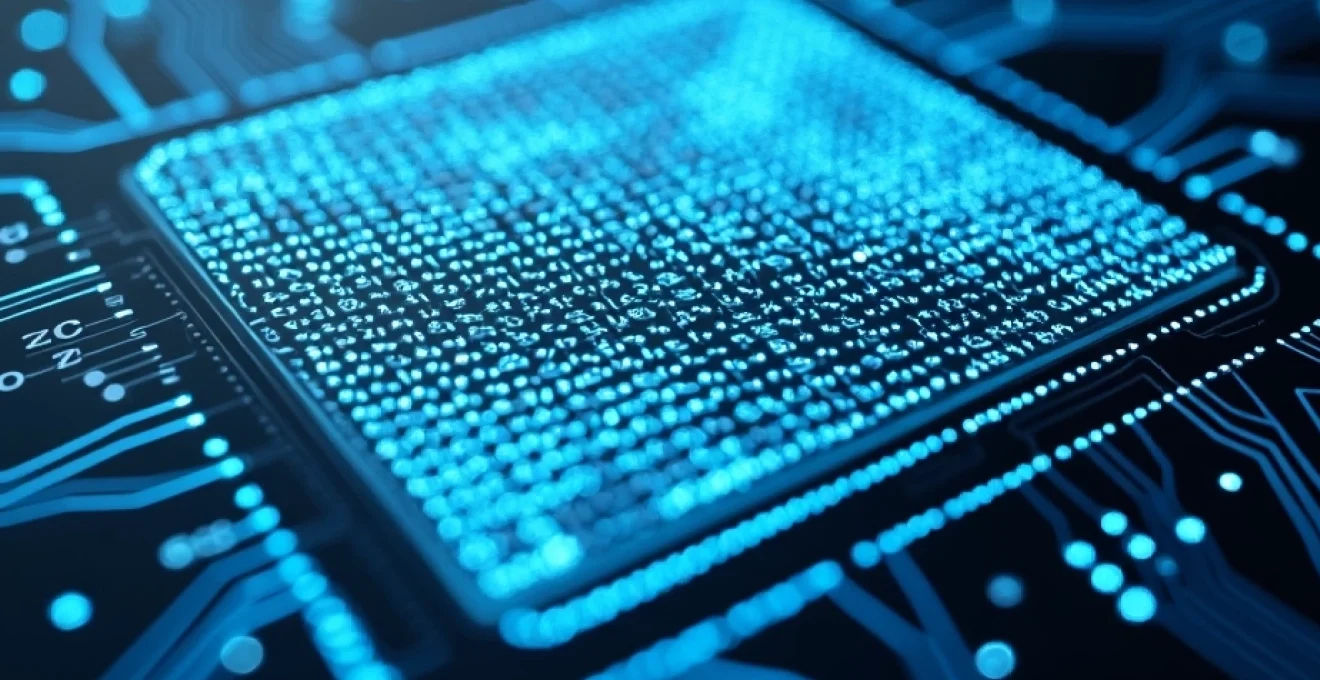
Il mondo dell’elettronica è in continua evoluzione, spingendo i confini della miniaturizzazione e delle prestazioni. Al centro di questa rivoluzione troviamo i PCB HDI (High-Density Interconnect), una tecnologia che sta ridefinendo le possibilità nel design dei circuiti stampati. Questi circuiti altamente sofisticati offrono una densità di connessioni senza precedenti, consentendo la realizzazione di dispositivi sempre più compatti e potenti. Ma cosa rende i PCB HDI così speciali e perché dovresti considerarli per i tuoi prossimi progetti?
Tecnologia HDI: principi e vantaggi per circuiti ad alta densità
La tecnologia HDI rappresenta un salto qualitativo nella progettazione dei circuiti stampati. A differenza dei PCB tradizionali, i circuiti HDI sfruttano tecniche avanzate per aumentare drasticamente la densità di interconnessioni. Questo si traduce in una maggiore funzionalità in spazi più ridotti, un aspetto cruciale nell’era dei dispositivi ultra-compatti.
Uno dei principali vantaggi dei PCB HDI è la capacità di ridurre significativamente le dimensioni complessive del circuito. Ciò non solo permette di creare dispositivi più piccoli e leggeri, ma migliora anche le prestazioni elettriche riducendo le lunghezze delle tracce e minimizzando i ritardi di propagazione. In termini pratici, questo si traduce in dispositivi che non solo sono più compatti, ma funzionano anche più velocemente e con maggiore efficienza.
Inoltre, la tecnologia HDI offre una flessibilità di design senza precedenti. Grazie alla possibilità di utilizzare vias e microvias di dimensioni estremamente ridotte, i progettisti hanno molta più libertà nel posizionamento dei componenti e nel routing delle tracce. Questo permette di ottimizzare il layout del circuito in modi che sarebbero impossibili con tecnologie tradizionali.
La vera forza dei PCB HDI risiede nella loro capacità di coniugare prestazioni elevate e miniaturizzazione estrema, aprendo nuove frontiere nel design elettronico.
Struttura e design dei PCB HDI
Microvie e fori laser: componenti chiave HDI
Al cuore della tecnologia HDI troviamo le microvie, fori microscopici che connettono i vari strati del circuito. Queste strutture, create con precisione millimetrica tramite laser, hanno diametri che possono scendere fino a 50 micron o meno. La loro caratteristica principale è quella di non attraversare l’intero spessore del PCB, ma di connettere solo gli strati adiacenti.
Le microvie possono essere classificate in diverse tipologie:
- Microvie cieche: connettono uno strato esterno a uno o più strati interni
- Microvie sepolte: connettono esclusivamente strati interni
- Microvie impilate: una serie di microvie sovrapposte che attraversano più strati
L’utilizzo di queste strutture miniaturizzate permette di aumentare drasticamente la densità di interconnessioni, liberando spazio prezioso sulla superficie del PCB per il posizionamento dei componenti. Inoltre, le microvie offrono vantaggi elettrici significativi, riducendo l’induttanza parassita e migliorando l’integrità del segnale ad alte frequenze.
Strati di build-up e core: architettura stratificata
La struttura di un PCB HDI è caratterizzata da un’architettura stratificata complessa, composta da strati di build-up e un core centrale. Il core, generalmente realizzato in materiale FR-4, fornisce la stabilità meccanica necessaria e ospita le connessioni attraverso l’intero spessore del PCB.
Gli strati di build-up, realizzati con materiali dielettrici ad alte prestazioni, vengono aggiunti sequenzialmente su entrambi i lati del core. Questa tecnica, nota come sequential lamination, permette di creare strutture estremamente dense e precise. Ogni strato di build-up può ospitare microvie e tracce ultrasottili, aumentando progressivamente la complessità e la densità del circuito.
Una tipica configurazione HDI potrebbe includere:
- 1-2 strati di build-up su ciascun lato del core
- Microvie che connettono gli strati esterni a quelli interni
- Vias tradizionali che attraversano il core per connessioni a lungo raggio
Questa struttura stratificata offre una flessibilità senza precedenti nel routing dei segnali, permettendo di ottimizzare il percorso di ogni traccia per minimizzare lunghezze e interferenze.
Tecniche di routing avanzate per HDI
Il routing in un PCB HDI richiede un approccio completamente diverso rispetto ai circuiti tradizionali. Le tecniche avanzate di routing sfruttano appieno le possibilità offerte dalle microvie e dalla struttura stratificata per creare layout estremamente densi ed efficienti.
Alcune delle tecniche più utilizzate includono:
- Via-in-pad : posizionamento delle microvie direttamente nei pad dei componenti
- Dogbone routing : utilizzo di microvie sfalsate per aumentare la densità di routing
- Fine-line routing : utilizzo di tracce ultrasottili (fino a 50 μm o meno)
Queste tecniche, combinate con software di progettazione avanzati, permettono di creare layout che sarebbero semplicemente impossibili con tecnologie tradizionali. Il risultato è una densità di interconnessioni che può superare le 500 connessioni per centimetro quadrato, un valore impensabile per i PCB standard.
Materiali innovativi per substrati HDI
La scelta dei materiali gioca un ruolo cruciale nelle prestazioni dei PCB HDI. I substrati tradizionali come l’FR-4, sebbene ancora utilizzati in alcune applicazioni, mostrano i loro limiti quando si tratta di alte frequenze e densità estreme.
Per questo motivo, l’industria sta adottando sempre più materiali avanzati specificamente progettati per applicazioni HDI. Alcuni esempi includono:
- Laminati a bassa perdita come il PTFE e il LCP per applicazioni ad alta frequenza
- Materiali ceramici ad alta permettività per una maggiore miniaturizzazione
- Substrati flessibili per applicazioni che richiedono conformabilità
Questi materiali offrono caratteristiche elettriche superiori, come costanti dielettriche più stabili e minori perdite, essenziali per garantire l’integrità del segnale in circuiti ad alta densità e alta frequenza.
La combinazione di materiali innovativi e tecniche di fabbricazione avanzate sta spingendo i confini di ciò che è possibile realizzare con i PCB HDI, aprendo nuove possibilità in settori come le telecomunicazioni 5G e l’elettronica di consumo di prossima generazione.
Applicazioni e settori chiave per PCB HDI
Smartphone e wearable: miniaturizzazione estrema
Il settore degli smartphone e dei dispositivi wearable è forse quello che ha beneficiato maggiormente della tecnologia HDI. La costante spinta verso dispositivi più sottili, leggeri e potenti ha trovato nella tecnologia HDI un alleato fondamentale. I moderni smartphone utilizzano PCB HDI con fino a 20 strati in uno spazio incredibilmente ridotto, permettendo di integrare fotocamere ad alta risoluzione, processori potenti e batterie di lunga durata in dispositivi spessi pochi millimetri.
Nel campo dei wearable, come smartwatch e fitness tracker, la tecnologia HDI ha letteralmente reso possibile l’esistenza di questi dispositivi. La capacità di creare circuiti estremamente compatti e conformabili ha permesso di integrare funzionalità avanzate in form factor indossabili, rivoluzionando il modo in cui interagiamo con la tecnologia nella vita quotidiana.
Apparecchiature mediche: precisione e affidabilità
Nel settore medicale, i PCB HDI stanno giocando un ruolo cruciale nell’evoluzione di dispositivi diagnostici e terapeutici. La miniaturizzazione resa possibile dalla tecnologia HDI ha portato allo sviluppo di apparecchiature portatili ad alta precisione, come ecografi palmari e monitor cardiaci indossabili.
Un esempio emblematico è rappresentato dai moderni pacemaker, che grazie ai PCB HDI hanno raggiunto dimensioni incredibilmente ridotte mantenendo al contempo funzionalità avanzate e una lunga durata della batteria. La densità di interconnessioni offerta dalla tecnologia HDI permette di integrare sensori sofisticati, processori potenti e sistemi di comunicazione wireless in dispositivi impiantabili di dimensioni minime.
Aerospaziale e difesa: prestazioni in ambienti estremi
Nel settore aerospaziale e della difesa, i PCB HDI trovano applicazione in sistemi avionici, radar e satellitari. La capacità di creare circuiti ad alta densità e alte prestazioni in formati compatti è essenziale per ridurre peso e dimensioni delle apparecchiature, un fattore critico in applicazioni aerospaziali.
Inoltre, la tecnologia HDI offre vantaggi significativi in termini di affidabilità e resistenza agli ambienti estremi. La riduzione delle lunghezze delle tracce e l’utilizzo di materiali avanzati contribuiscono a migliorare la resistenza alle vibrazioni, agli shock termici e alle radiazioni, aspetti cruciali per l’elettronica destinata a operare nello spazio o in ambienti militari critici.
Sfide di progettazione e fabbricazione HDI
Gestione termica in layout ad alta densità
Uno dei principali ostacoli nella progettazione di PCB HDI è la gestione efficace del calore. L’elevata densità di componenti e interconnessioni può portare a concentrazioni di calore localizzate, potenzialmente dannose per l’affidabilità e le prestazioni del circuito. Per affrontare questa sfida, i progettisti devono adottare strategie avanzate di gestione termica, come:
- Utilizzo di materiali a elevata conducibilità termica
- Implementazione di vias termiche per dissipare il calore verso strati dedicati
- Ottimizzazione del layout per una distribuzione uniforme del calore
Inoltre, l’uso di strumenti di simulazione termica avanzati è diventato essenziale per prevedere e mitigare i punti caldi prima della fabbricazione del PCB.
Controllo dell’impedenza e integrità del segnale
Mantenere un controllo preciso dell’impedenza e garantire l’integrità del segnale diventa particolarmente complesso nei PCB HDI, dove le tracce sono estremamente ravvicinate e le frequenze operative possono raggiungere diversi GHz. Le sfide principali includono:
- Minimizzazione del crosstalk tra tracce adiacenti
- Controllo delle riflessioni dovute a discontinuità di impedenza
- Gestione dei ritardi di propagazione in strutture multi-layer complesse
Per affrontare queste sfide, i progettisti devono fare affidamento su tecniche avanzate di routing e su strumenti di simulazione elettromagnetica per ottimizzare il layout e garantire prestazioni ottimali ad alte frequenze.
Tecniche di produzione avanzate: MSAP e mSAP
La fabbricazione di PCB HDI richiede tecnologie di produzione all’avanguardia per raggiungere le tolleranze e le precisioni necessarie. Due tecniche che stanno rivoluzionando la produzione di PCB HDI sono il Modified Semi-Additive Process (MSAP) e il modified Semi-Additive Process (mSAP).
Queste tecnologie permettono di creare tracce e spazi estremamente fini, con larghezze che possono scendere fino a 30 μm o meno. Il processo MSAP, in particolare, offre vantaggi significativi in termini di precisione e ripetibilità, essenziali per la produzione di massa di PCB HDI ad alte prestazioni.
Tuttavia, l’adozione di queste tecnologie pone sfide significative in termini di investimenti in attrezzature e controllo di processo. I produttori devono implementare sistemi di controllo qualità estremamente rigorosi per garantire la consistenza e l’affidabilità dei PCB HDI prodotti con queste tecniche avanzate.
Analisi costi-benefici dell’implementazione HDI
L’adozione della tecnologia HDI comporta inevitabilmente un aumento dei costi di produzione rispetto ai PCB tradizionali. Tuttavia, un’analisi attenta rivela che i benefici possono spesso superare i costi aggiuntivi, specialmente in applicazioni ad alte prestazioni o dove la miniaturizzazione è un fattore critico.
I principali fattori da considerare in un’analisi costi-benefici includono:
- Riduzione delle dimensioni complessive del dispositivo
- Miglioramento delle prestazioni elettriche
- Potenziale riduzione del numero di strati necessari
- Maggiore flessibilità di design e time-to-market più rapido
In molti casi, l’adozione di PCB HDI può portare a risparmi significativi in altre aree del processo produttivo, come l’assemblaggio e il packaging, compensando l’aumento dei costi del PCB stesso.
È importante sottolineare che i costi della tecnologia HDI stanno gradualmente diminuendo man mano che le tecniche di produzione maturano e si diffondono. Ciò sta rendendo l’HDI una
opzione sempre più accessibile e competitiva per un’ampia gamma di applicazioni.
Futuro dei PCB HDI: tendenze e innovazioni emergenti
Il futuro dei PCB HDI appare estremamente promettente, con diverse tendenze e innovazioni che stanno plasmando l’evoluzione di questa tecnologia. Una delle direzioni più interessanti è lo sviluppo di PCB HDI flessibili e conformabili, che aprono nuove possibilità in settori come l’elettronica indossabile e l’Internet delle Cose (IoT). Questi PCB ultrasottili e flessibili possono adattarsi a superfici curve o essere integrati direttamente nei tessuti, rivoluzionando il concetto di elettronica indossabile.
Un’altra area di intensa ricerca è l’integrazione di componenti passivi direttamente nel substrato del PCB. Questa tecnologia, nota come “componenti integrati”, promette di ridurre ulteriormente le dimensioni dei circuiti eliminando la necessità di componenti discreti sulla superficie del PCB. Immaginate un resistore o un condensatore che non occupa spazio sulla scheda perché è letteralmente parte del substrato stesso!
La miniaturizzazione continua a spingere i limiti della tecnologia HDI. Si prevede che nei prossimi anni vedremo l’adozione diffusa di tracce e spazi inferiori a 30 μm, con alcune applicazioni di punta che potrebbero raggiungere i 15 μm o meno. Questa ulteriore riduzione delle dimensioni permetterà di creare dispositivi ancora più compatti e potenti, aprendo nuove frontiere in settori come la realtà aumentata e virtuale, dove la miniaturizzazione è cruciale.
L’evoluzione dei PCB HDI sta ridefinendo i confini tra elettronica tradizionale e tecnologie emergenti, gettando le basi per una nuova era di dispositivi interconnessi e intelligenti.
Un’altra tendenza significativa è l’integrazione sempre più stretta tra PCB HDI e tecnologie di packaging avanzate come il System-in-Package (SiP) e il 3D-IC. Queste soluzioni ibride permettono di combinare la flessibilità dei PCB HDI con l’estrema miniaturizzazione offerta dal packaging a livello di wafer, creando sistemi elettronici altamente integrati e performanti.
Infine, non possiamo ignorare l’impatto che l’intelligenza artificiale e il machine learning avranno sulla progettazione dei PCB HDI. Algoritmi avanzati di ottimizzazione del layout e routing automatico stanno già rivoluzionando il processo di design, permettendo di creare layout ottimizzati che sfruttano appieno le potenzialità della tecnologia HDI. In futuro, potremmo vedere sistemi di AI capaci di generare autonomamente design di PCB HDI ottimizzati per specifiche applicazioni, riducendo drasticamente i tempi di sviluppo e migliorando le prestazioni complessive.